Two years have passed since the Circular NP – Better Circulation of Animal Manure project started. The idea of the project is to recycle nutrients in agriculture more efficiently and thus reduce the leakage of eutrophying substances to the Baltic Sea. Good for the environment and a potential new income for farmers. It sounds simple, but why hasn’t it already been done and how does it work?
The project is a collaborative effort between BalticWaters, the Swedish University of Agricultural Sciences (SLU) and the Research Institutes of Sweden (RISE). Athanasios Pantelopoulos, a researcher at the Department of Soil and Environment at SLU, specialises in soil nutrient cycling, which he has been researching since his PhD in Copenhagen. Now, 7 years later, he is investigating how the fertiliser value can be optimised in manure products recycled from either animal manure or digestate from biogas plants. But to understand why Athanasios is doing this research, we need to take a step back.
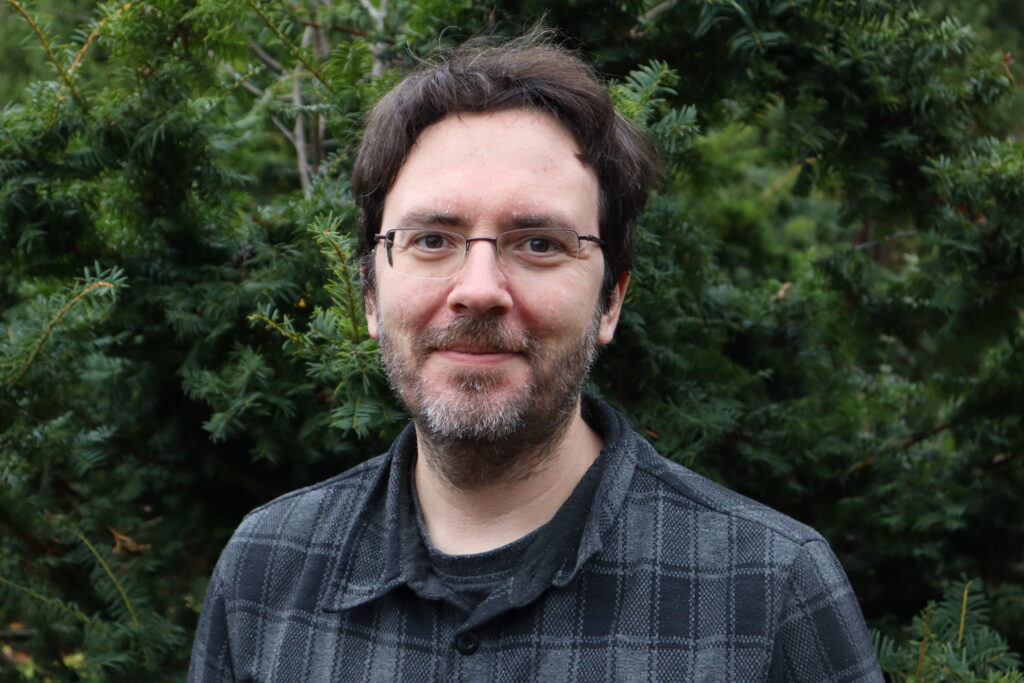
Athanasios Pantelopoulos. Foto: Amanda Öberg, SLU.
An imbalance that is problematic for agriculture and the environment
In Swedish agriculture, we currently have an uneven distribution of the important nutrients nitrogen and phosphorus. The uneven distribution is a consequence of the specialisation in agriculture that has taken place in recent decades. This specialisation has led to farms mainly producing crops or engaging in animal production. This in turn has led to entire regions focusing their production on either crop or animal production. The effect is to create an imbalance in nutrient availability, with crop farms having to rely on mineral fertilisers, while livestock farms often have a surplus of nutrients in animal manure produced on the farm. When large livestock farms are unable to utilise the surplus nutrients in crop production, this can lead to nutrient leakage into nearby water bodies and ultimately the Baltic Sea. One answer to the problem could be to transport animal manure from farms with a surplus to farms with a deficit. However, animal manure contains a lot of water and is heavy, resulting in high transport costs. It is therefore not cost-effective to transport animal manure over long distances. It is precisely this problem that Athanasios and his colleagues in the Circular NP project are trying to resolve.
Researchers are working on finding technical solutions to extract nutrients from animal manure and digestate from biogas plants. In this way, they can create a fertiliser material that is circular, biological and cost-effective to transport over long distances – from areas with a nutrient surplus to areas with a deficit.
The role of nitrogen and phosphorus in plants
Plants need nitrogen to form shoots and leaves. Lack of nitrogen results in pale and weak plants. The plant takes up nitrogen in the form of ammonium and nitrate, but most of the nitrogen is bound in the soil’s humus.
Phosphorus is necessary for the plant’s photosynthesis, flowering, seeding and growth. For the plant to absorb the phosphorus, it must be in the form of phosphate.
– Digestate and animal manure contain phosphorus, nitrogen, potassium and organic matter that the soil and crops need – a resource in itself! If we can separate the nutrients from livestock manure and digestate and make them available to plants, and tailor the dose to the needs of a specific crop, it could create an opportunity for an organic fertiliser market. It could hopefully replace much of the mineral fertiliser used today – while reducing the risk of nutrient leakage to lakes and seas,” says Athanasios.
Heat as a tool
Circular NP is conducted in the Kalmar region where animal production is high and there is a surplus of phosphorus. Both digestate from the farmer-owned biogas plant More Biogas and animal manure directly from nearby farms are used in the experiments. The first step in the process is to separate the liquid from the digestate/animal manure into a lighter, dry fraction that is rich in phosphorus and contains a lot of organic material. At the same time, a heavy, wet fraction is formed that contains the majority of the nitrogen and potassium.
Separation methods
The project evaluates mechanical and chemical mechanical separation. Mechanical separation is done with a screw press and centrifuge that separates digestate/animal manure into a wet and a dry fraction. In chemical mechanical separation, chemicals are first added to facilitate separation and then mechanical separation of digestate/animal manure is used. The project tests polymer and ferric chloride for chemical flocculation. Chemical flocculation helps to collect small particles so that they can be mechanically separated in the next step.
– The dry fraction, formed after mechanical separation, still consists of as much as 60-70% liquid. It is both heavy to transport and bulky to store in anticipation of spring fertilisation. The dry content therefore needs to be further increased to create a product that is cost-effective to transport and that does not risk starting to compost due to too high a liquid content. During composting, greenhouse gases and ammonia are released, which means that the substrate loses its fertilising value. By further reducing the liquid content of the dry fraction, the product can be more easily transported and stored without losing its fertilising value, says Athanasios.
The best way to get rid of additional liquid in the dry fraction is through heat, so Athanasios will test five heat treatment methods to increase the fertiliser value of the dry fraction:
Bio-drying (low heat treatment). Microorganisms break down the carbon in the digestate/animal manure creating heat, which in turn drives off the liquid in the dry fraction. Bio-drying cannot remove all the water, so the final product is still not optimal for long distance transport. The remaining product is mostly phosphorus-rich organic material that can increase the soil content, especially in degraded soils.
Drying. The substrate is dried at temperatures between 80-100 °C and the final product becomes a powder that can be pelletised and then easily used by the farmer. The disadvantage is that some nitrogen is released due to the heat. Possibly, acidification before drying can minimise the loss of nitrogen.
HTC. Hydrothermal carbonisation (HTC) is a type of wet carbonisation or pyrolysis that takes place under high pressure and temperatures between 200-220 °C. Further studies are needed to determine whether the carbon and phosphorus are more or less stable than in the other products.
Pyrolysis. The substrate is treated at high temperatures, between 400-800°C. To prevent the dry fraction from being burnt to ash and losing all its carbon, the treatment is carried out in an oxygen-free environment. The end product is called biochar and has the great advantage that almost all the liquid has disappeared while neither phosphorus nor carbon has been lost, but unfortunately most of the plant-available nitrogen is lost. The carbon is stable, but the method can lead to phosphorus not being available to plants. An important part of the continued tests will therefore be to find the optimal treatment temperature that does not make the phosphorus unavailable to the plants. Biochar can also have positive effects on the physical properties of the soil.
Combustion. Treatment takes place at high temperatures, under oxygen-rich conditions, so that all organic matter is oxidised and the end product is ash. All the phosphorus remains in the ash but the nitrogen has been lost.
Nitrogen volatility the biggest challenge
The heavy, nitrogen-rich wet fraction will never be cost-effective to transport over long distances. Instead, the project aims to treat the wet fraction to make it the best possible fertiliser for nearby farms. A major challenge is that nitrogen is volatile and can easily escape into the air in the form of ammonia and greenhouse gases. When these substances escape, the fertiliser value decreases and the environment is negatively affected. Erik Sindhöj, a researcher at RISE, is investigating methods to stabilise nitrogen. Three different methods are being tested within the project:
N2 Applied. Using a plasma arc, in an enclosed environment, the bond between the nitrogen molecules in the nitrogen gas in the air is broken, which then binds with oxygen to form a nitric oxide (NOx) compound. The air, now high in NOx, is adsorbed in the wet fraction so that NOx can further oxidise to NO2 (nitrite) and NO3 (nitrate). Under low pH, NO3 binds with ammonium nitrogen to become ammonium nitrate, which is relatively stable. In addition to stabilising the nitrogen in the wet fraction, the amount of plant-available nitrogen in the slurry has also doubled.
Acidification with sulphuric acid. Sulphuric acid lowers the pH of the wet fraction. The aim is to reduce the pH below 6 as the nitrogen becomes more stable. The researchers therefore add sulphuric acid to the wet fraction to a level where the nitrogen is sufficiently stable while still being available to plants.
Incorporation of ammonium sulphate liquid. Ammonium sulphate liquid is a by-product of a technique being tested to reduce the ammonium content in the digester. High ammonium levels in the digester inhibit biogas production. By mixing ammonium sulphate liquid into the wet fraction, the researchers will investigate whether ammonia loss and methane emissions are reduced during the storage period.
– The goal is to find a technique that reduces ammonia loss during storage and spreading of the wet biofertiliser, while increasing the amount of nitrogen that the plants can absorb. If we succeed, the wet bio-fertiliser product can reduce the need for mineral nitrogen, says Erik.
The project’s bio-fertiliser should be as effective as mineral fertiliser
The phosphorus-rich, dry, and the nitrogen-rich, wet, bio-fertiliser products will be evaluated in different experiments.
The dry bio-fertiliser products are first tested in so-called incubation trials. During incubation trials, the fertiliser product is mixed with soil in small cups to see how the material breaks down in the soil. The researchers then measure the amount of nitrogen and plant-available phosphorus released to the soil and how much carbon dioxide is released. The researchers also examine how the soil pH is affected by each fertiliser product. The incubation trials give the researchers an indication of which products have the greatest potential and can proceed to potted trials.
During the pot experiments, the bio-fertiliser product is mixed into a pot of soil in which nutrient-rich plants, such as grass, are planted. As the dry bio-fertiliser products contain a small amount of nitrogen, mineral nitrogen needs to be added to meet the needs of the crop. The grass is allowed to grow and then harvested 2-3 times over a four-month period. The harvest is analysed to see how much nitrogen and phosphorus the plant has taken up from the soil. The results will be compared with pot experiments where mineral phosphorus has been used to draw conclusions about the effectiveness of the bio-fertiliser.
The biofertiliser products that show the best results in the pot trials will later be tested and evaluated in full-scale field trials. The nitrogen-rich, wet biofertiliser products will be tested directly in field trials and compared with ordinary, untreated biofertiliser.
Long but important journey
The hope is that researchers in the Circular NP project will develop a phosphorus-rich bio-fertiliser product that can be transported over longer distances and is at least as effective as mineral phosphorus. The goal is also to develop a nitrogen-rich, wet bio-fertiliser product that can be used on neighbouring farms. The journey is long and winding, but it is important.
– If we can return more nutrients from animal manure to agriculture, we can both reduce nutrient leakage and create added value for farmers where the surplus manure, which has been a problem in the past, can become a profitable product, says Konrad Stralka, Executive Director of BalticWaters.
For this to be profitable, farmers, agricultural advisors and food producers need to be involved.
– We are conducting this research project to develop biofertiliser products that are as effective as conventional fertilisers. But if the products are not used, they are of no use, so it is very important to discuss with farmers and stakeholders, says Konrad.
Athanasios agrees.
– Circular NP is a big project, but projects on this scale that include science and communication with stakeholders and actors are completely lacking at the EU level, so the project feels particularly important, says Athanasios.
Incubation trials are currently underway, and in the spring, the project’s researchers hope to begin potting trials. We look forward to the results with excitement!

Want to know more about Circular NP? Take a look here.